DC Gear Motor Micro Small Low Speed Large Torsion Permanent Magnet 24V XD37GB3530 Bracket(200rpm/min )
Description
Item Type: DC Gear Motor Model: XD-37GB3530 Material: Copper Output Shaft Size: Approx. 5.5 x 15mm / 0.2 x 0.6in Insulation Resistance: After the rated operation of the motor under normal temperature and humidity when measuring the insulation resistance between the coil and the motor shell with a DC500V resistance meter it does not exceed 20MΩ Insulation Withstand Voltage: After the rated operation of the motor under normal temperature and humidity 50Hz or 60Hz is applied between the coil shells for one minute and the abnormality is 1500V. Temperature Rise: It is normal to install a gear box or equivalent heat sink and conduct rated operation under normal temperature and humidity by using the resistance method to measure the temperature rise of the coil below 70℃ Insulation Class: Class B(130℃) Operating Environment Temperature: Motor: -10~+40℃ (no icing) Use Environment Humidity: 85% or less (no condensation) CW/CCW: Yes Speed Adjusted: Yes Model Voltage(DC/V) No-Load Speed (rpm/min) No-Load Current(A) Rated Torsion(kg/cm) Load Speed (rpm/min) Load Current(A) Power(W) XD-37GB3530 24 100 0.09 4 93 0.34 10 200 0.09 2 175 0.34 10 300 0.09 1.8 245 0.34 10 500 0.09 0.8 435 0.34 10 600 0.09 0.5 353 0.34 10 Notes: 1 Overload and Locked Rotor: When the motor is running it generates heat due to the energy conversion that occurs inside the coil and the iron core and the temperature gradually rises. The load is within the rated range and the heat generation and heat dissipation are balanced and the coil of the motor will not be burnt. However it will cause heat under overload and locked-rotor conditions. When the running time is too long the insulating film on the enameled wire of the coil is dissolved causing a short circuit between the enameled wires and burning the motor. 2 When Running at Low Speed: For DC motors carbon brushes are generally used. The rotating commutator rubs against the carbon brushes creating sparks at the notches of the commutator. When the motor is running at a low speed the carbon brush powder that is easily generated by the friction between the commutator and the carbon brush will accumulate in the commutator slot causing a short circuit and burning the motor and driver. Please be very careful. 3 Precautions on the PWM Controller: When using the PWM controller the carbon brushes have a shorter service life than in the rated voltage (or fixed voltage) state. In addition depending on the frequency of use carbon brushes may wear out quickly. The frequency of PWM control of DC motors is generally 10-20KHz and repeated ON-OFF during PWM control can save energy. However the parts used in the motor are similar to the frequency of use which will cause resonance and heat. Please pay full attention to use. In the PWM control state when using the built-in motor of the electrolytic capacitor the motor may not rotate at a certain fixed frequency. Please try to use varistor to hide the motor. (Need to do related tests) 4 Regarding Inertia and Braking: After the motor is powered off the rotor will still rotate due to inertia which is the inertia of the DC motor. If you want to stop the rotation immediately you can short-circuit the positive and negative terminals after turning off the power. The use of this kind of brake is to use the motor to generate electricity (reverse current). The current may increase temporarily and shorten the life. 5 Treatment of Floor Motor: Because the magnetic tile is a brittle material the DC motor may break the magnetic tile once it falls causing the motor to block and cause burns. Please do not use the motor after it has landed at a high altitude.
Price history chart & currency exchange rate
Customers also viewed
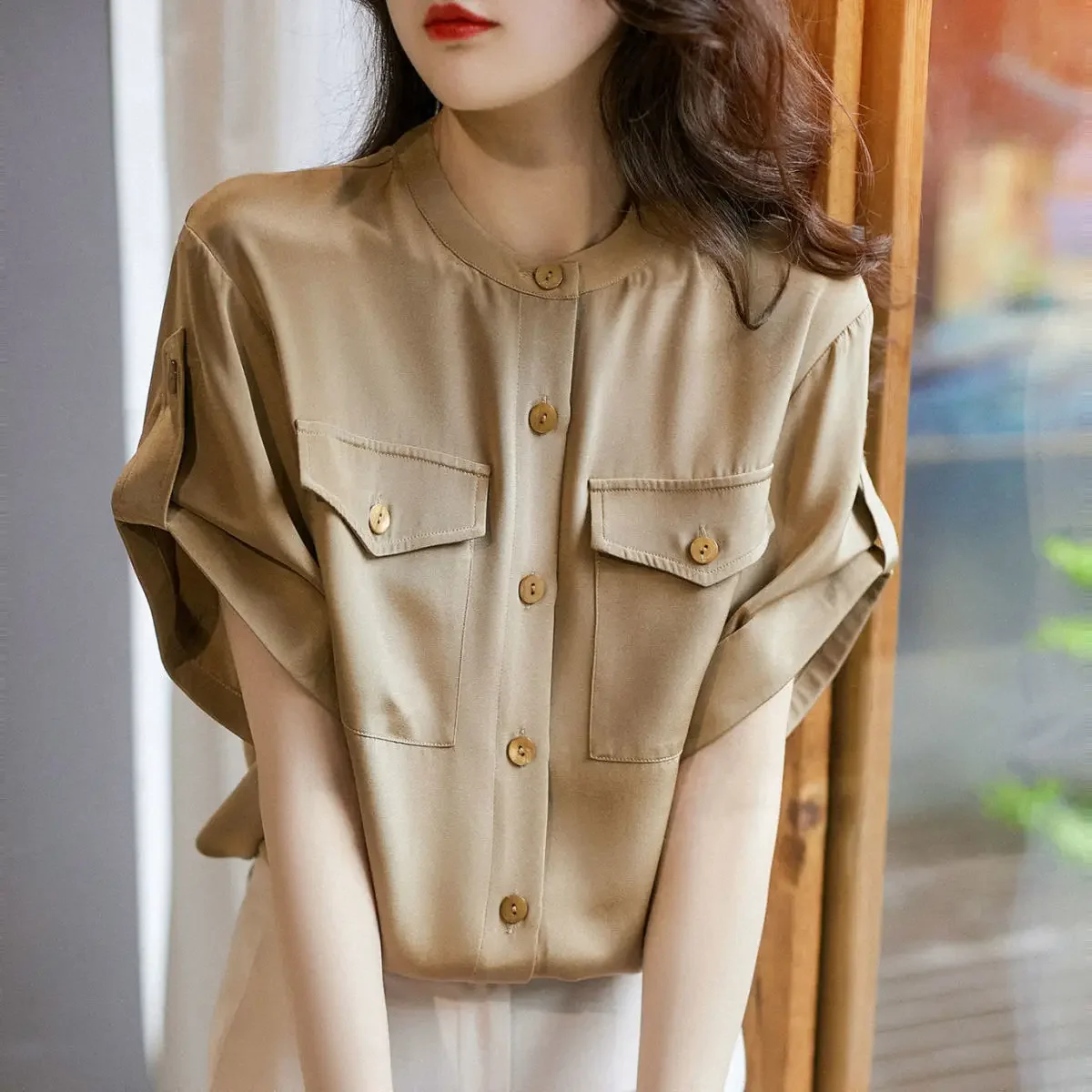
$14.97
New white dress dress dress summer license date dress dresses for women party clothing women dress for women
aliexpress.com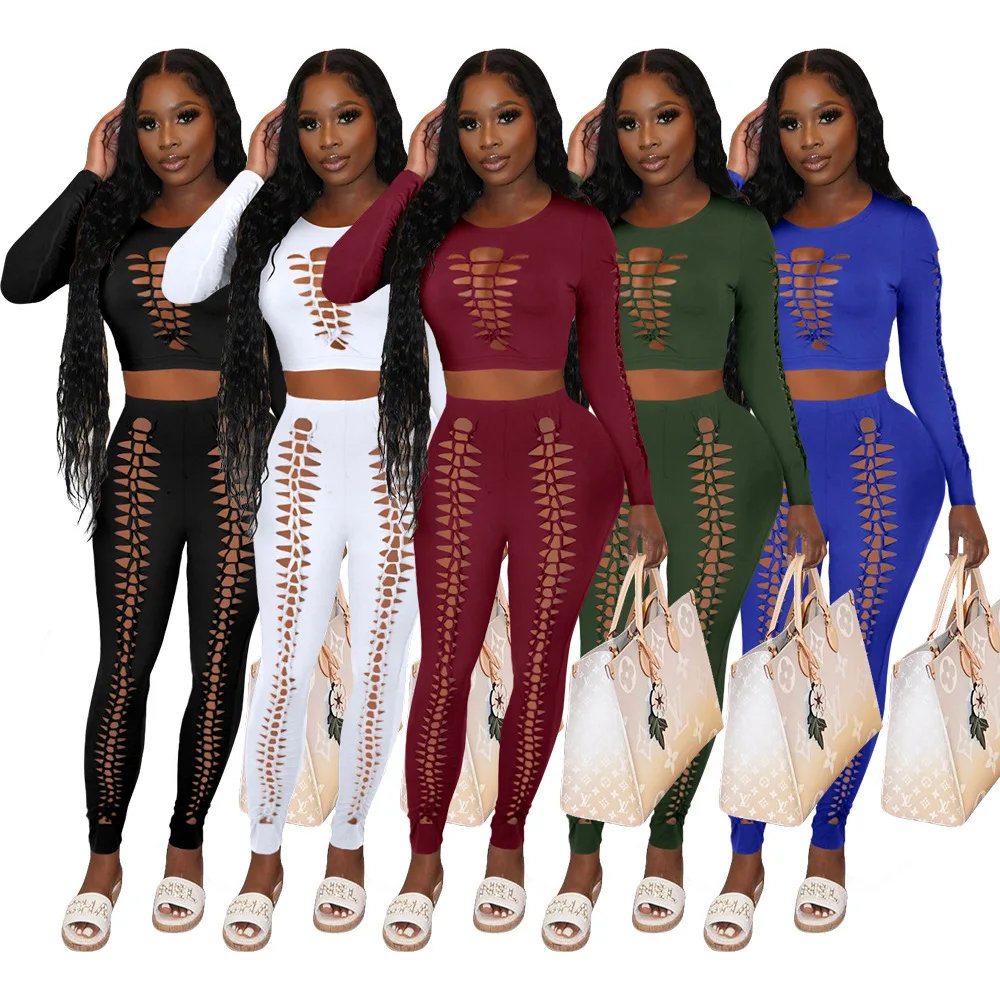
$19.49
Однотонные комплекты из 2 предметов с длинным рукавом с вырезами, женский сексуальный короткий топ, облегающие леггинсы, модная Повседневная Клубная одежда для женщин
aliexpress.ru
$10.78
Автомобильная аудиопанель 2Din, лицевая панель, рамка для Great Wall Haval H1/M4 10,1 дюйма, большой экран, радио, стереопанель, крепление для приборной па...
aliexpress.ru
$26.50
Charging Base Gamepad Charger Dual Charger for PS3 USB Cable for Sony PlayStation 3 Controller Console The Plane Charge Games
aliexpress.com
$81.45
Новый фрикционный комплект пластин сцепления коробки передач 4F27E для FORD Focus MAZDA 3 6
aliexpress.ru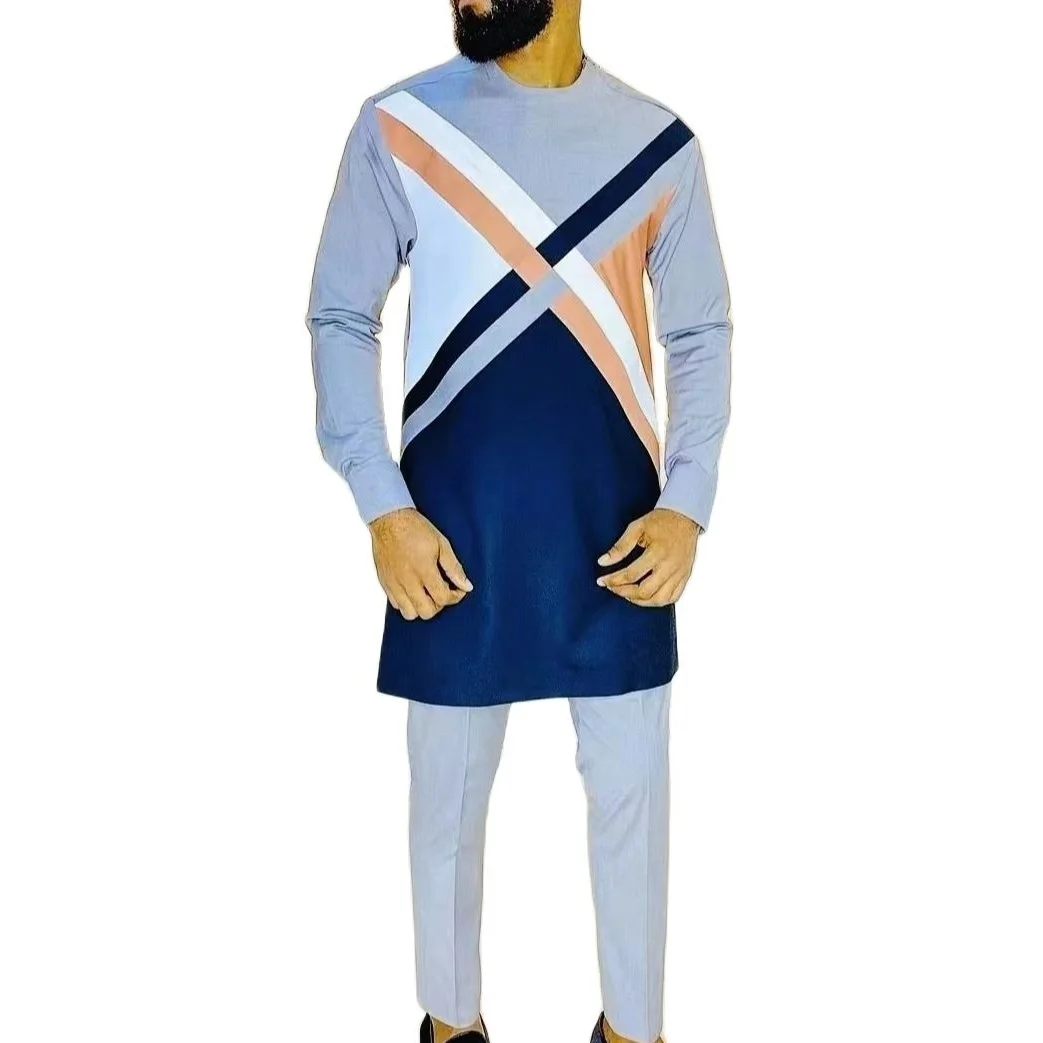
$31.57
Костюм мужской параллельный и перекрестный из хлопка, Однотонная рубашка в стиле пэчворк, цвет темно-синий/белый/оранжевый
aliexpress.ru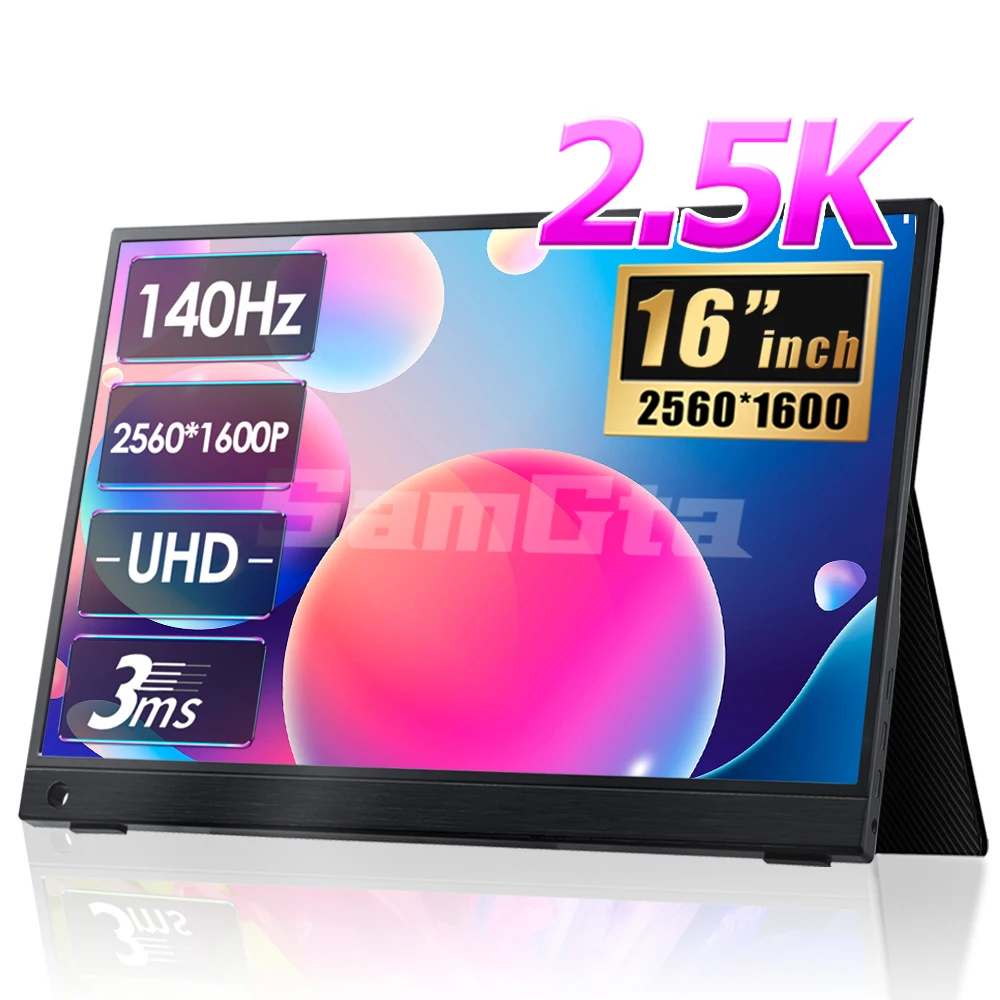
$265.62
16-дюймовый 2,5 K портативный монитор 144 Гц/60 Гц 2560*1600 16:10 100% sRGB дисплей игровой экран для ноутбука Mac Phone Xbox PS4/5 Switch Pc
aliexpress.ru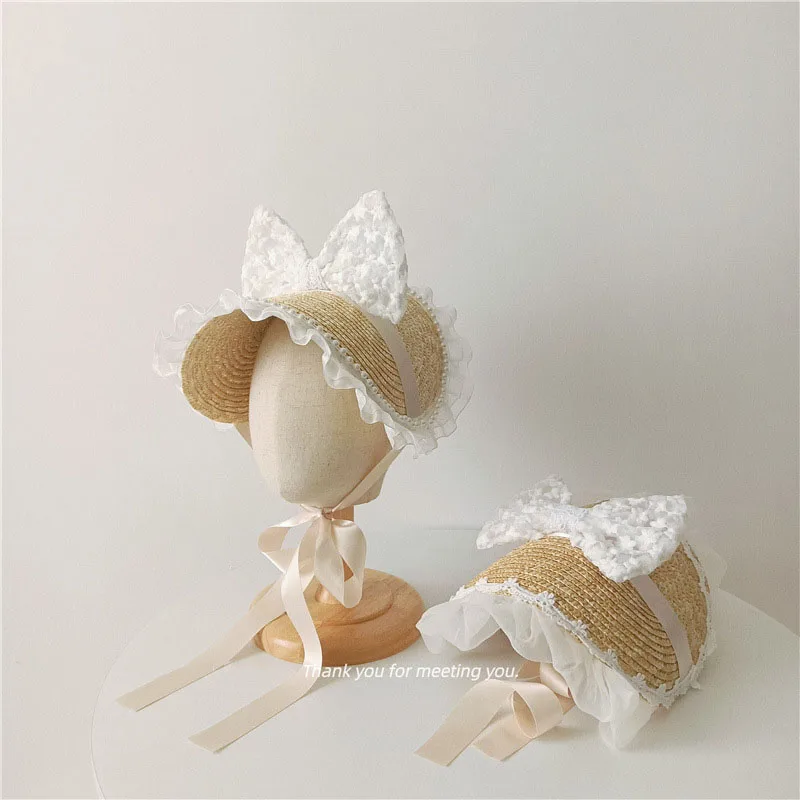
$8.68
Кружевная соломенная шляпа принцессы для девочек с милым бантом реквизит для фотосъемки новорожденных 2023 летняя детская Солнцезащитная шляпа с защитой от УФ-лучей
aliexpress.ru
$109.99
Женский деловой костюм Blingbling, облегающий блейзер с отложным воротником на одной пуговице и брюки с корсетом, Офисная Женская одежда
aliexpress.ru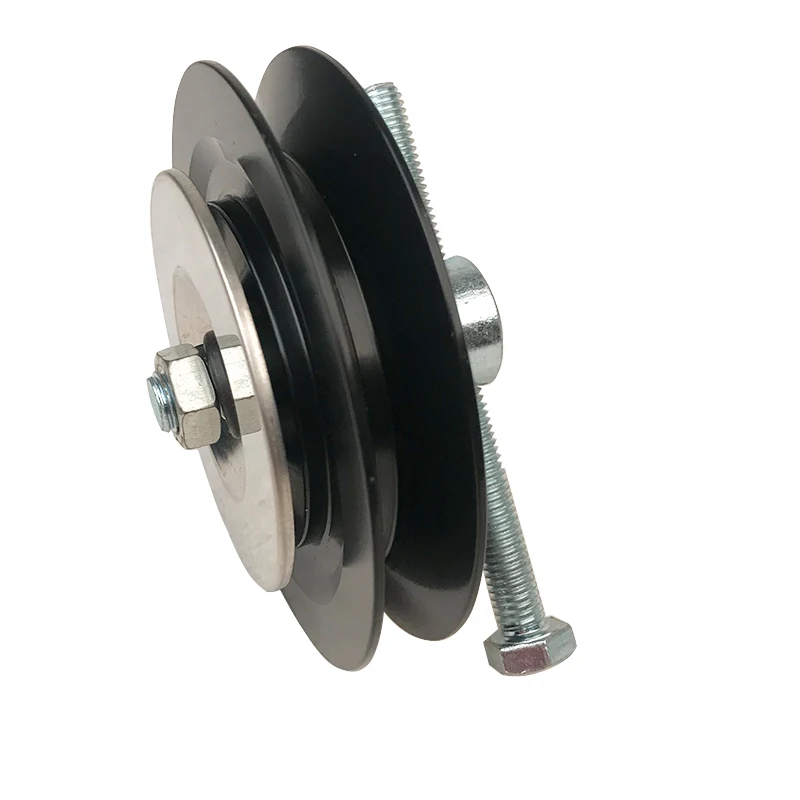
$21.90
Натяжитель шкива направляющей автомобиля 88440-35010, 7813A136, 2 л/3 л/1KZ/1HD/2C/3C/4M41, для Land Cruiser, Prado Lite, Ace, Noah Town, Ace, Hiace
aliexpress.ru
$26.20
Электрический дверной замок защелка привода в сборе для Chevy GMC Suburban Yukon S-15 Safari и т. Д. Передний правый пассажирский боковой замок 16631626
aliexpress.ru
$22.47
4 кнопки, Черный Автомобильный брелок для ключей для Toyota Tacoma Highlander Sequoia Tundra Rav4, сменный пульт дистанционного управления для автомобильного ключа, чехол, аксессуары
aliexpress.ru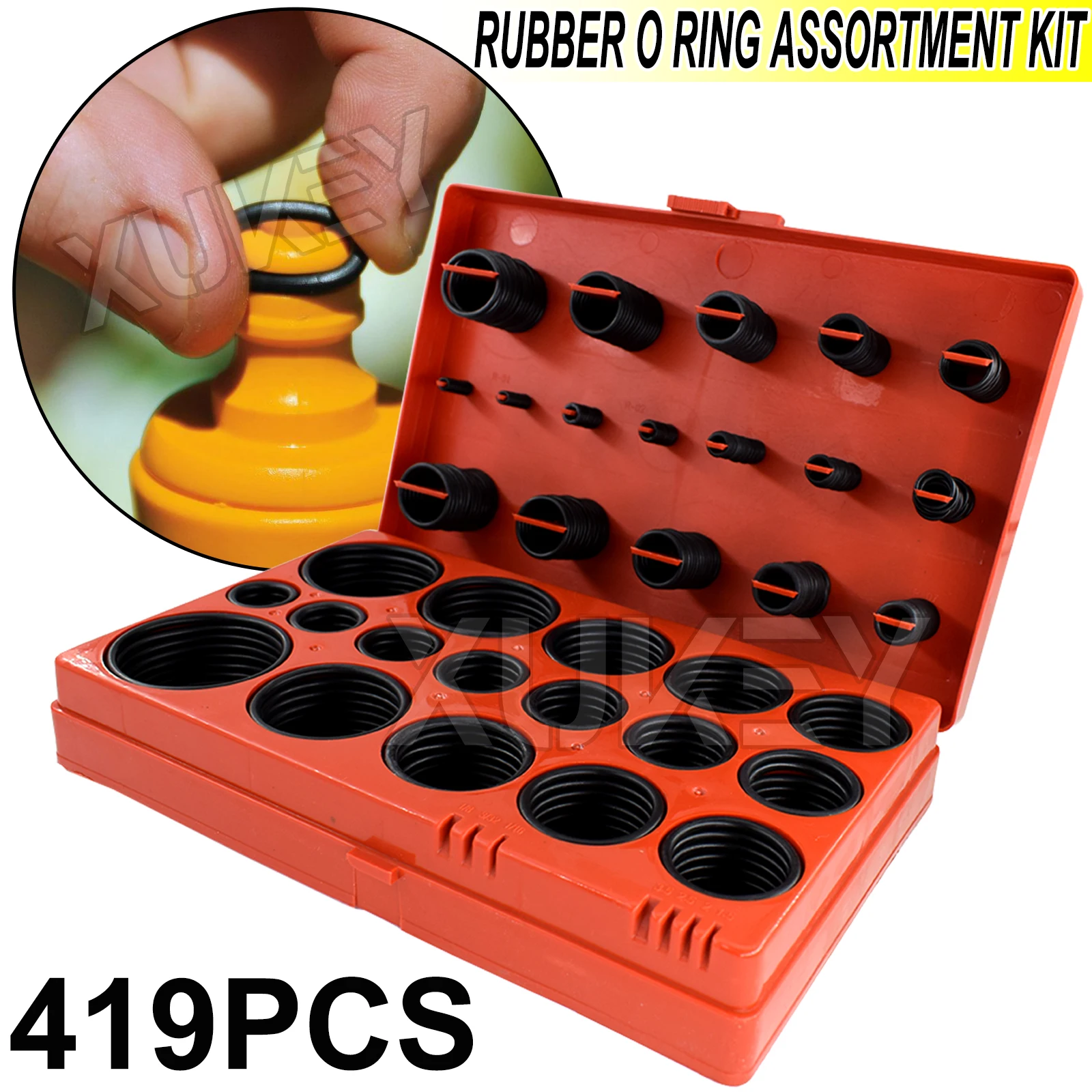
$20.74
419 шт. набор универсальных уплотнительных колец резиновые метрические втулки комплект уплотнительных колец коробка уплотнительная прокла...
aliexpress.ru
$32.26
433 МГц TPMS датчик давления в шинах 4 шт. 68157568AA 68239720AC для 2014 2015 2016 Dodge Ram 1500 2500 3500 Jeep Cherokee
aliexpress.ru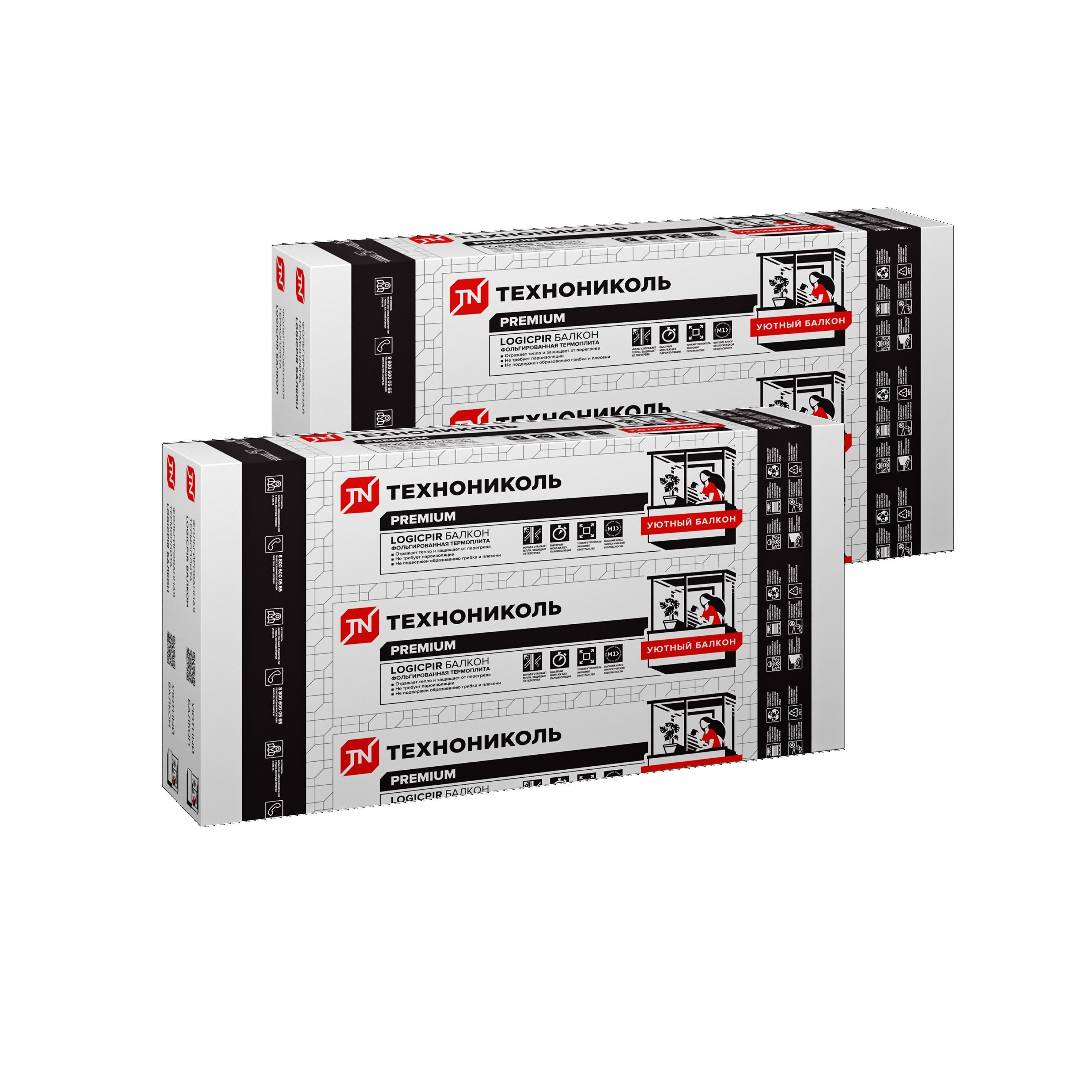
$177.46
Плита теплоизоляционная Технониколь LOGICPIR Балкон Ф/Ф L-кромка 1190х590х40 мм, 2 упак., LOGICPIR Балкон Ф/Ф
goods.ru
$109.12
european station men's shoes air cushion small white shoes men's summer new breathable thick-soled casual shoes men's trendy shoes inner heightened s
fordeal.com
$88.38
2023 autumn and winter new chelsea boots for women couples large size boots women's genuine leather short boots
fordeal.com
$47.76
thick-soled sandals women's casual shoes women's white shoes 2023 new summer hollowed out breathable sports and leisure sneakers
fordeal.com
$54.99
Высокое качество, фабрика, оптовая продажа, профессиональный штатив для камеры, для цифровой камеры, смартфона, подставка для камеры Gopor
aliexpress.ru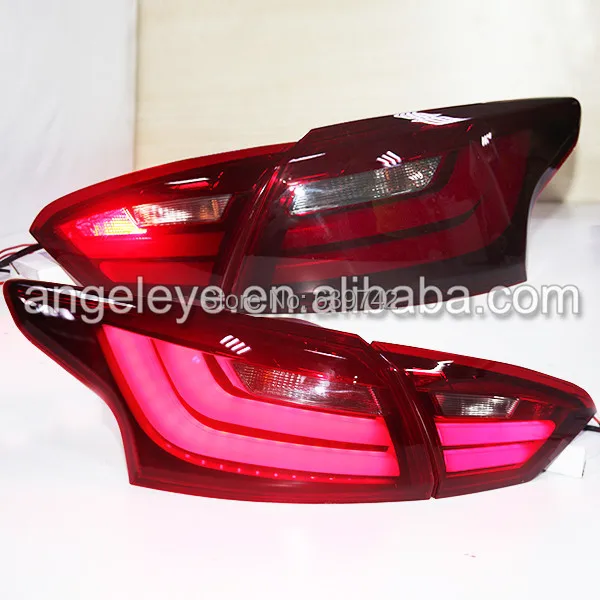
$288.88
2014-2014 год, светодиодная лента для FORD Focus 3 Sedan, задние фонари, задние фонари для BMW, стиль, темно-красный цвет
aliexpress.ru
$27.93
Электрический измельчитель чеснока 150 мл, мини-кухонный комбайн, прессы, измельчитель лука, Masher, портативный блендер, резак, измельчитель
aliexpress.ru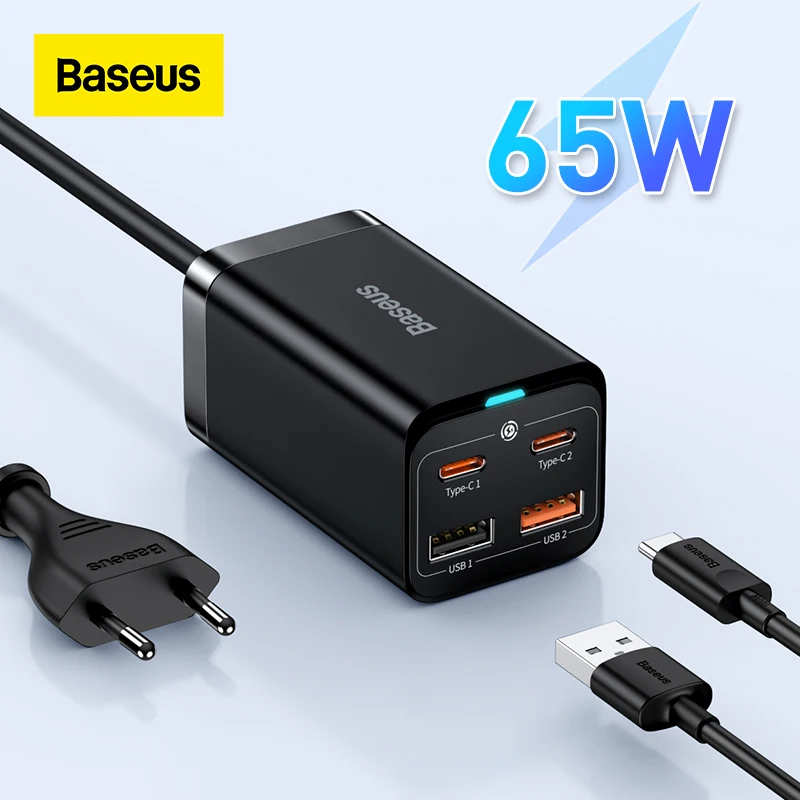
$41.93
Baseus 65W GaN3 Pro Fast Charger Quick Charge 3.0 USB Type C PD For iPhone 12 13 11 Pro Sumsung Xiaomi
aliexpress.ru
$7.42
Transparent PVC Pencil Bag Canvas Flower 20cm Stationery Storage Pencil Case Waterproof Pencil Pouch School Student Supplies
aliexpress.ru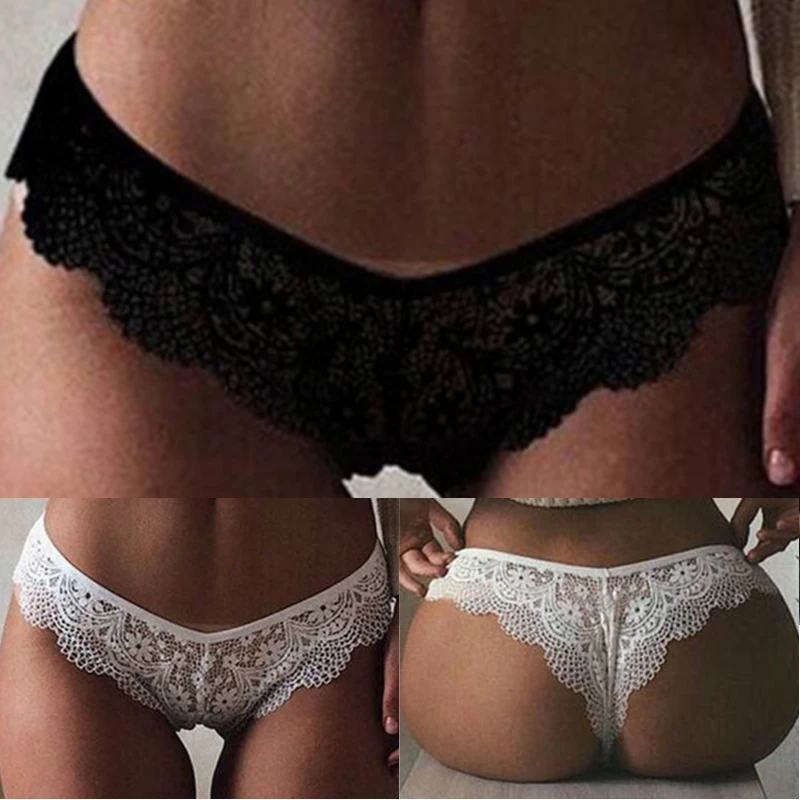
$0.06
Женское сексуальное нижнее белье, кружевные прозрачные брифы, Трусики с высокой талией, ультратонкие ажурные стринги, однотонные брюки
aliexpress.ru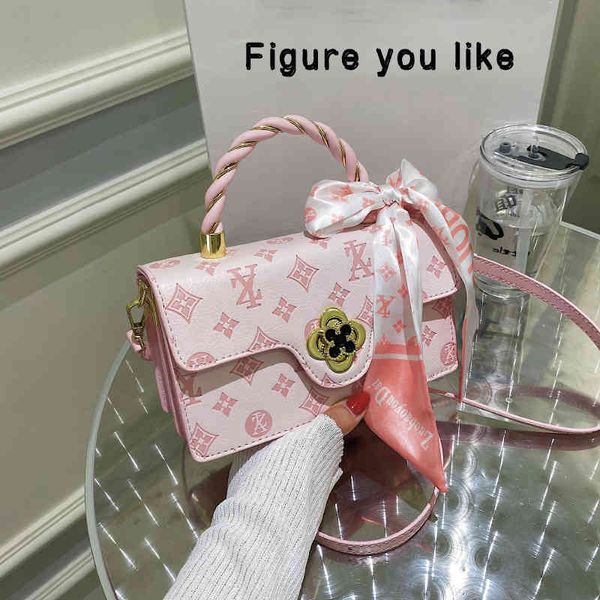
$65.23
2022 factory wholesale new bag female fashion portable messenger net red foreign style one shoulder small square bag
dhgate.com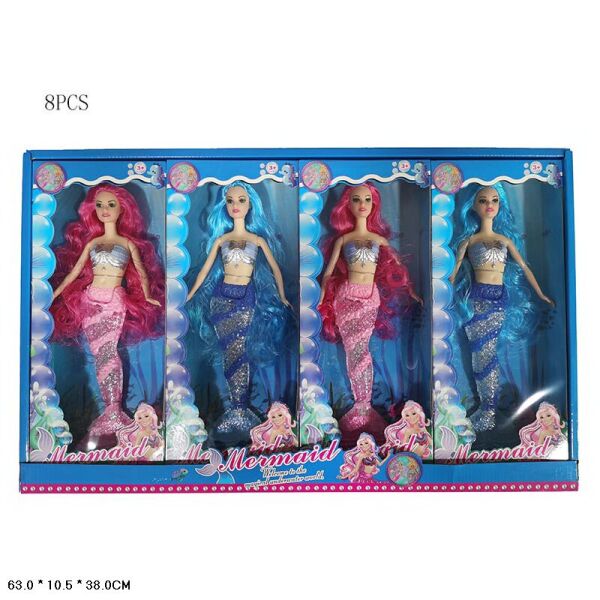
$5.11
Кукла 30см русалка муз., свет., 2 цвета, ЦЕНА ЗА 1ШТ, В УП. 8ШТ, в корр. 63*10,5*38см (12/96шт)
allo.ua